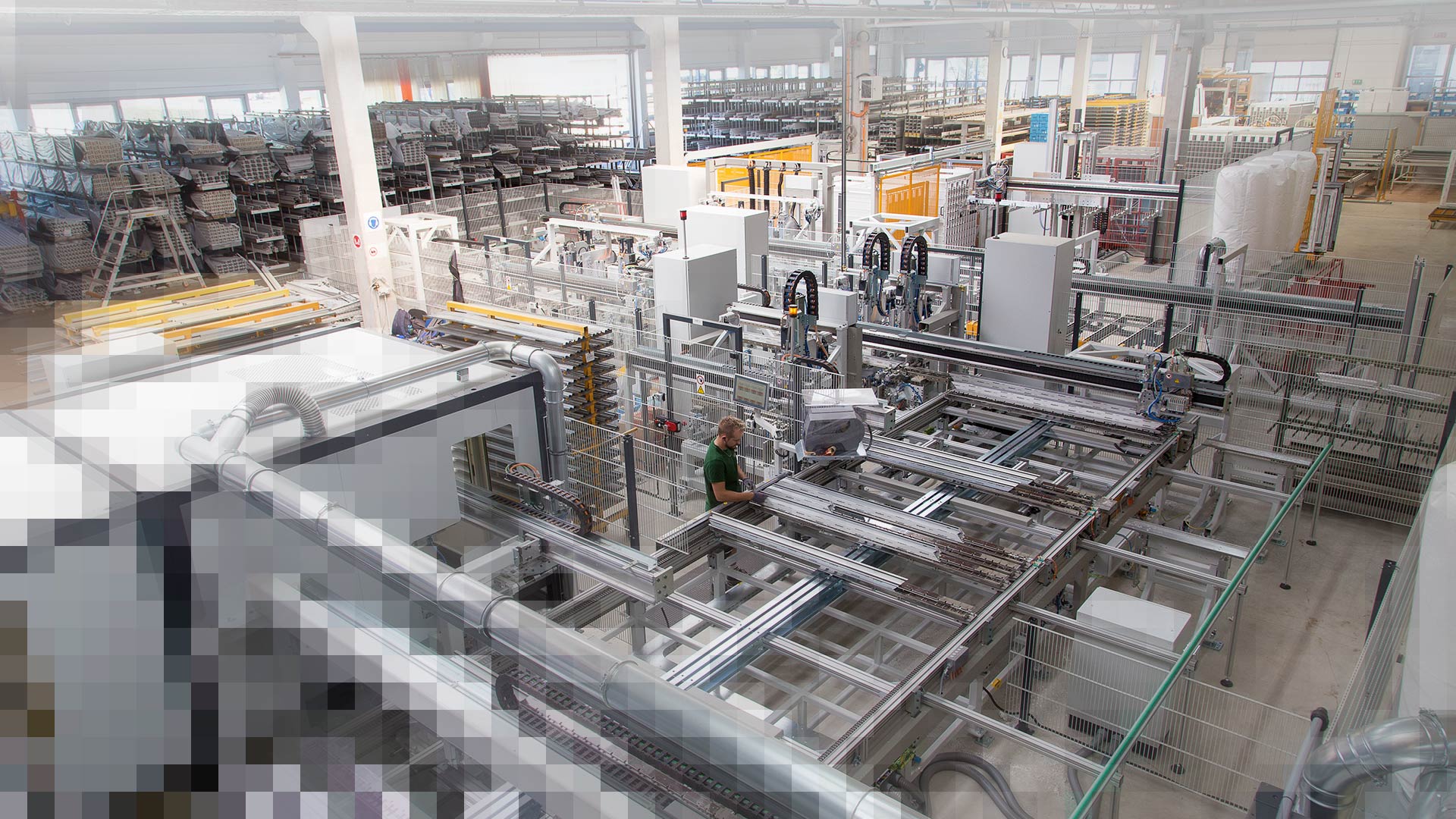
Für den nächsten
Automatisierungsschub
gesorgt
Ein in die Jahre gekommenes Bearbeitungszentrum durch ein deutlich flexibleres ersetzen.
Damit nicht nur eine ganze Reihe manueller Nachbearbeitungen überflüssig machen und einen Mitarbeiter einsparen, sondern auch die Kapazität um 35 Prozent erhöhen. Erreicht hat die ideal Fensterbau Weinstock GmbH all das mit der Investition in ein neues Zuschnitt- und Bearbeitungszentrum vom Typ BAZ 1000-orbit 8/ VU „Medium“ aus dem Hause Schirmer, das mit zwei Konturfrässtationen sowie Stabbearbeitungszentren zur Verschraubung beziehungsweise für die Bearbeitung in Stahl sowie einem Sortierer mit automatischer Abstapelung ergänzt wurde.
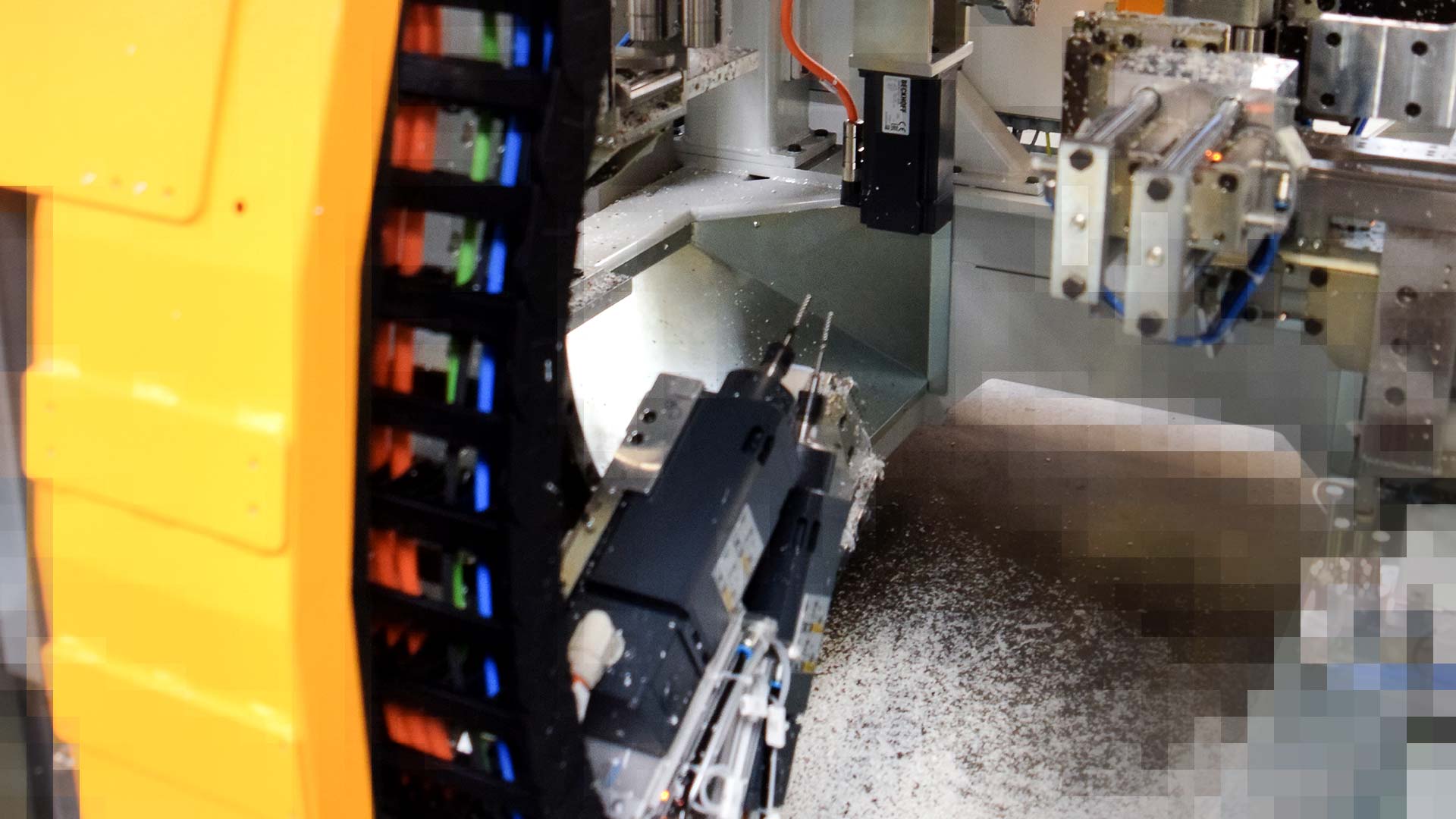
Die beiden Fräs- und Bohrmotoren auf jedem der zwei C-förmigen Bearbeitungsmodule umkreisen das Profil, was eine Bearbeitung aus jedem Winkel heraus möglich macht.
„Mit dem neuen BAZ werden eine ganze Reihe von manuellen Arbeitsschritten überflüssig, die beispielsweise für die Ausfräsung des Mittelsteges oder bei Pfostenverbindungen, das Ausklinken von Dichtungen, für Bohrungen für Absturzsicherungen etc. noch nötig waren. Diese mussten bisher auf gesonderten Arbeitstischen erfolgen. Dank des neuen BAZ sind die Proile jetzt komplett fertig bearbeitet, wenn sie in den Fächerwagen einsortiert werden“, beschreibt Geschäftsführer Stefan Weinstock die wesentlichen Veränderungen.
Fritz J. Bentrup, Geschäftsführer des Maschinenlieferanten hebt dagegen auf die besondere Flexibilität der Anlage ab: „Weitere Profile können ohne Weiteres ins Programm aufgenommen werden. Denn dafür ist keine Umrüstung an den Auflagen und Spannern nötig. Die zunehmende Digitalisierung wird zudem dazu führen, dass immer mehr mechatronische Komponenten in Fenstern verbaut werden. Hierfür werden zusätzliche Bohrungen und Fräsungen nötig sein, was mit der von uns konzipierten Anlage kein Problem darstellt.“
Die Anlage im Detail
Bedient wird die gesamte Anlage durch einen Mitarbeiter, nur zeitweise unterstützt von einem Kollegen, der das Auflegen der Profile übernimmt. Hierzu muss er lediglich die Profile aus den in unmittelbarer Nähe zum BAZ positionierten Profilpaletten auf das automatische Vorlegemagazin ziehen. Die gesamte Anlage hat sich bereits mit den automatisch einstellbaren Profilführungen an die Profilkonturen angepasst. Produziert werden auf der Anlage Fenster und Fenstertüren aus den Systemen Ideal 4000, 5000, 7000 und 8000 von aluplast.
Die 16 Jahre alte Anlage hingegen wird jetzt im Sonderbau für die Bearbeitung von Profilen für Hebeschiebetüren, Haustüren sowie sonstige Sonderprofile genutzt. Die Bearbeitung der PVC-Profile erfolgt auf der neuen Anlage durch insgesamt vier Bearbeitungsmotoren, die frei beweglich auf zwei C-Schienen positioniert sind. Dies macht ein Umkreisen der Profile und eine Bearbeitung in allen Winkeln möglich. Durch gleichzeitig ablaufende lineare und rotierende Bewegungen über acht Achsen können die Werkzeuge auf kürzesten Wegen in Position gebracht werden.
Ausgeführt werden dabei die folgenden Bearbeitungen:
- Entwässerungs- und Belüftungsschlitze /-bohrungen im Blendrahmen, Flügel, Pfosten, Kämpfer und Sprossen
- Schlosskasten-Ausfräsung am Flügel
- Anbringen von Schließteil-Markierungsbohrungen
- Markierungsbohrungen für von innen verschraubbare Pfosten-, Kämpfer- und Sprossenverbindungen
- Rollladennippel-Bohrungen bzw. Clip-Markierungen
- Ausfräsungen für Lüfter
- Zurückstanzen der Dichtungen bei Einsatz von Lüftern oder Kämpfern
- Zurückfräsen der powerdur-Stege bei energeto-Profilen.
- Integrierte Werkzeugbruch-Kontrolle
Das BAZ ist wie die nachfolgenden SBZs zur Bearbeitung im Stahl mit einer Werkzeugbruchkontrolle ausgestattet, die über die Stromaufnahme der Fräsmotoren in Abhängigkeit der Bearbeitungen realisiert wird. Nach dem Zuschnitt durch die VU-Sägeeinheit mit Doppelsägeaggregat zum gleichzeitigen Sägen von An- und Abschnitt sowie Klinkschnitt werden die Profile bei Bedarf den beiden Frässtationen zugeführt, um stirnseitige Fräsungen für Pfosten-, Kämpfer und Sprossenkonturen anzubringen und die Hinterfräsung der Dichtungsnut vorzunehmen. „Mit dem Einsatz von zwei Frässtationen ist gewährleistet, dass auch in diesem Bereich die Taktzeit eingehalten werden kann. Die Frässtationen sind wie ein Roboter programmierbar, so dass für die unterschiedlichen Bearbeitungen nur ein Werkzeugwechsel nötig ist“, macht Bentrup deutlich. Hierfür stehen insgesamt zwölf Werkzeugplätze zur Verfügung. Der Werkzeugwechsel erfolgt automatisch.
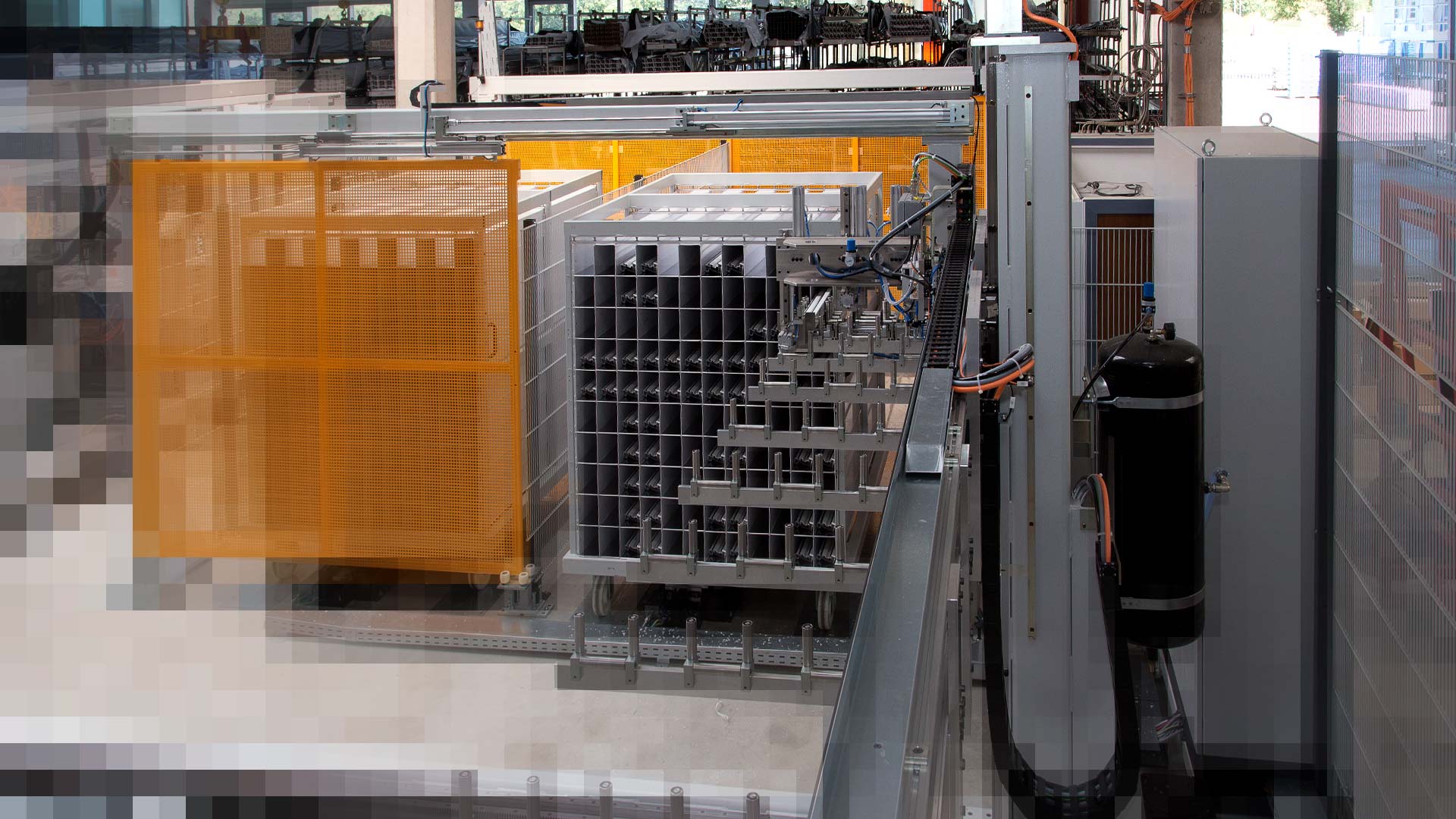
Die automatische Stabsortieranlage nimmt bis zu drei Profilstäbe auf und sortiert diese in einen der bereit stehenden Fächerwagen ein.
Querförderer fungieren als Puffer
Im Anschluss daran werden die Rahmenteile über einen Horizontal-Umlauf-Puffer der Stahleinschubstation zugeführt. Diese ermöglichen einen taktunabhängigen Transport zwischen den Bearbeitungszentren und erzielen so eine gleichmäßige Auslastung aller Maschinenbereiche. Ein zweiter dieser Puffer kommt im Bereich der Stahlbearbeitung zum Einsatz. „Damit erreichen wir, dass die Bearbeitungsstationen die fertigen Teile immer abgeben können und es nicht zu Staus in der Produktion kommt. „Mit einem Produktivitätsgewinn von 25 bis 30 Prozent ist der Effekt beachtlich“, macht Bentrup deutlich. Ideal hat sich auf Grund des geringen Anteils armierter Fenster für den manuellen Stahleinschub entschieden, die exakte Positionierung übernimmt ein „Stahleinschub-Finger“. Für die Verschraubung kommen drei drehmoment- und tiefenüberwachte Schraubaggregate mit Servomotoren zum Einsatz. Diese sind in der Lage, auch zwei verschiedene Schraubentypen parallel zu verarbeiten. Für sämtliche Bohrungen im armierten Profil kommt eine CNC-gesteuerte Bohrstation mit drei Achsen zum Einsatz.
Sonderlösung für Mitteldichtungssteg
Eine Besonderheit der Anlage ist die Frässtation für die Freifräsung des Mittelsteges bei Festverglasungen. „Mitteldichtungssysteme haben bei uns einen Anteil zwischen 70 und 80 Prozent. Hinzu kommt ein hoher Anteil von Kombinationen von Drehkippfenstern mit Festverglasungen. Bisher mussten wir die Teile für diese Elemente ausschleusen und den Mittelsteg mit Hilfe einer Oberfräse wegfräsen, was neben dem zeitlichen Aufwand auch mit einer hohen Lärmbelastung verbunden war“, berichtet Weinstock.
Die fertig bearbeiteten Profilstäbe werden über eine Sortierweiche an die automatische Stabsortieranlage übergeben. Diese nimmt bis zu drei Stäbe gleichzeitig auf und sortiert diese in die zwei bereitstehenden Fächerwagen
ein. Ist der erste Fächerwagen komplett befüllt, kann dieser manuell entnommen werden. Ein Schutztor vor der Stabssortieranlage macht es möglich, dass dies bei laufender Anlage erfolgen kann.
Ausgelegt ist die Anlage auf eine Leistung von 203 einflügeligen Drehkipp-Fenstern oder 98 zweiflügeligen Drehkipp-Fenstern in einer Schicht von acht Stunden.
Zügige Inbetriebnahme
Die neue Anlage wurde im März geliefert. Vorbereitende Arbeiten wurden allerdings schon über den Jahreswechsel vorgenommen. Der mechanische Aufbau der gesamten Anlage habe zweieinhalb Wochen in Anspruch genommen, nach dreieinhalb Wochen hätten bereits die ersten Profile bearbeitet werden können. „Nach fünf Wochen liefen dann schon 98 Prozent der Profile über die neue Maschine“, berichtet ein sichtlich zufriedener Stefan Weinstock. „Das Projekt war freilich seitens der Familie Weinstock gut vorbereitet. Es gab seitens der verantwortlichen Monteure nicht einen Anruf, dass es Probleme mit der Integration der Anlage gäbe“, lobt Bentrup.
Ausbau der Kapazitäten nötig
Parallel dazu investiert das Unternehmen aber auch in die Produktion für Holzfenster am Standort in Traben-Trarbach. Momentan sind Holz- und Holz/Alu-Fenster so stark nachgefragt, dass es zu Lieferzeiten kommt, die die Geduld der Kunden auf die Probe stellen. Mit verantwortlich dafür waren die begrenzten Kapazitäten in der Oberflächenbeschichtung. Da qualifizierte Mitarbeiter ohnehin schon schwierig zu finden sind und für Arbeitsplätze in der Beschichtung noch viel weniger, hat sich das Unternehmen entschlossen die beiden Handspritzstände durch zwei Spritzroboter zu ersetzen. Diese werden aktuell montiert. Bei Inbetriebnahme wird die Erfassung der zu beschichtenden Elemente durch einen Scanner den Robotern die Informationen liefern, die nötig sind, um die Fensterkonturen exakt abzufahren. Diese können auch in den Pausenzeiten eigenständig arbeiten, was den gewünschten Zuwachs an Kapazität brächte. Zusätzlich zur Unicontrol Winkelanlage soll im nächsten Jahr eine kleine Conturex von Weinig die Produktion aufnehmen, um der starken Nachfrage gerecht zu werden und die Lieferzeiten zu reduzieren.
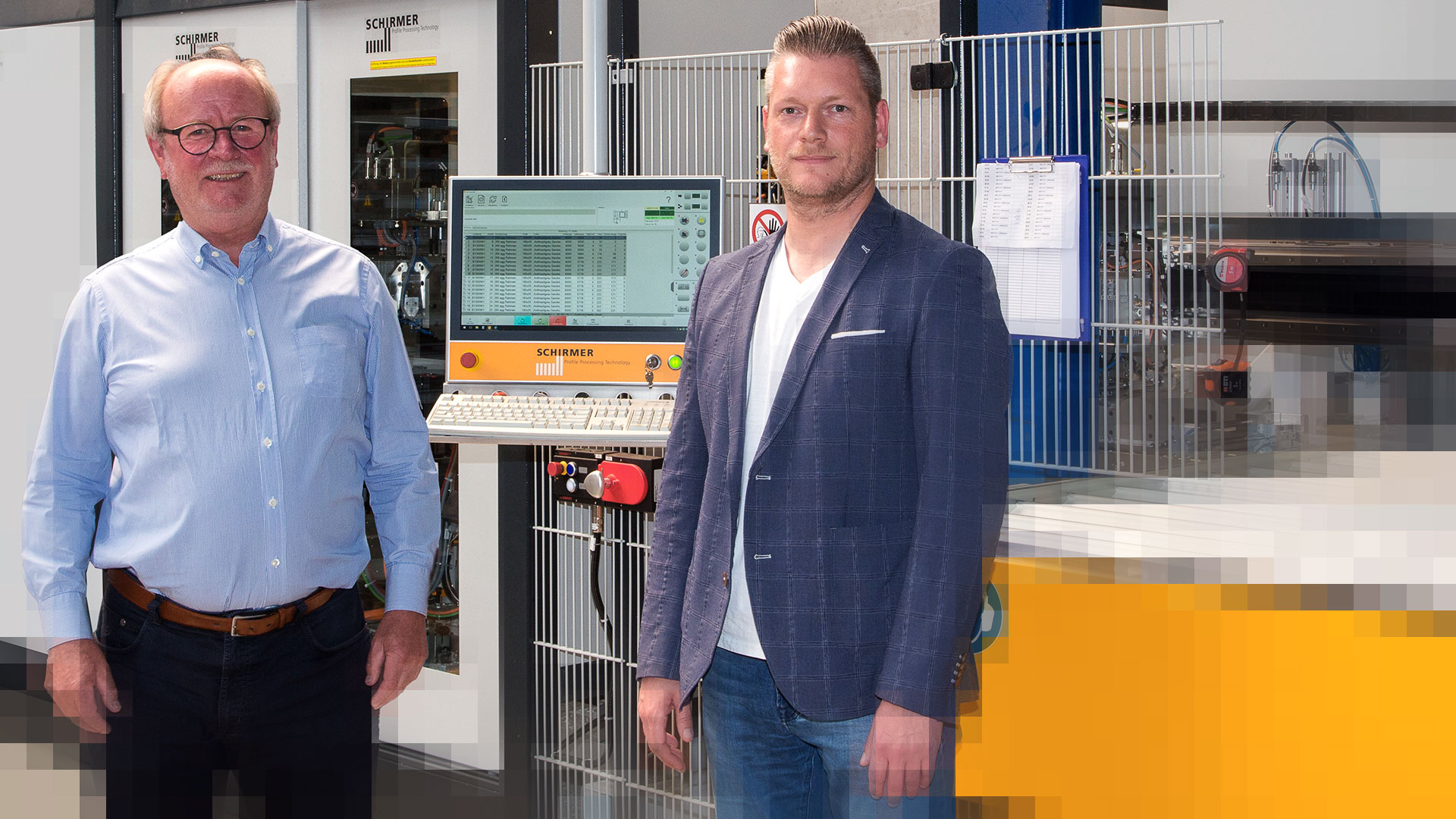
Zufriedene
Projektpartner
Zufriedene Projektpartner. Stefan Weinstock (rechts im Bild) und Fritz J. Bentrup.
Dieser Artikel erschien in der Zeitschrift Bauelemente Bau 09/20.